The implementation of the Building Safety Act 2022 has introduced a transformative framework for improving safety and accountability within the UK construction industry. To help industry professionals navigate these new requirements, two important guidance documents—Building Safety Advice Note 5: Implications for Quality Management and Building Safety Advice Note 6: Impact on Designers—outline crucial responsibilities and compliance measures.
These advice notes offer essential insights into how the Act affects quality management systems and the role of designers in ensuring building safety. Below is an overview of their key takeaways:
Advice Note 5: Implications for Quality Management
CLICK HERE TO DOWNLOAD
This document focuses on the impact of the Building Safety Act on quality management processes, emphasizing compliance, accountability, and competence. Key areas include:
-
The Dutyholder Regime: The Act designates specific dutyholders (e.g., clients, principal contractors, principal designers) responsible for ensuring that buildings comply with safety regulations. These responsibilities extend across all construction projects, with additional requirements for higher-risk buildings (HRBs).
-
Competence and Skills Verification: Quality management systems must now incorporate mechanisms to verify and document the competence of professionals involved in design and construction. Standards such as PAS 8671 and PAS 8672 outline required skill sets for principal designers and contractors.
-
Mandatory Reporting & Safety Assurance: A new mandatory occurrence reporting system requires that defects and safety concerns be reported immediately, ensuring early intervention and risk mitigation.
-
Liability and Enforcement: The Act imposes severe penalties, including imprisonment, for safety breaches. It extends the period for enforcement actions against defective work from 12 months to 10 years.
To ensure compliance, firms must review and update their quality management systems, strengthen risk assessment procedures, and develop a culture of accountability through training and continuous professional development (CPD).
Advice Note 6: Impact on Designers
CLICK HERE TO DOWNLOAD
Designers play a critical role in building safety, and this guidance highlights their increased responsibilities under the Act. Major aspects include:
-
New Compliance Requirements: Designers must ensure that their work aligns with the Building Regulations 2010 (as amended in 2023), incorporating safety principles from the early design stages.
-
Enhanced Competency Standards: Principal designers must demonstrate competence in fire safety and structural integrity, supported by documented evidence.
-
Golden Thread of Information: Designers must contribute to the “Golden Thread”—a comprehensive digital record of a building’s design, construction, and maintenance that remains accessible throughout its lifecycle.
-
Collaboration and Accountability: A cross-disciplinary approach is essential, with designers working alongside contractors and dutyholders to ensure compliance at all project stages.
Why These Advice Notes Matter
Both advice notes reinforce the urgent need for cultural and procedural changes within the industry. The Act’s reforms demand a proactive approach to safety, emphasizing risk management, competency verification, and regulatory compliance. For industry professionals, these documents provide practical steps to adapt to the new legal landscape and uphold the highest safety standards.
By integrating these insights into daily practice, designers and quality managers can help ensure safer, more resilient buildings while maintaining compliance with the evolving regulatory framework.
There’s a lot happening with procurement right now, which is opening opportunities for a more strategic approach by public clients.
The recent launch of the National Procurement Policy Statement and the Construction Leadership Council’s public sector procurement guidance, ‘Potential solutions to common evaluation issues faced by Clients in the built environment sector”, and the passing of the Procurement Act, are opening up opportunities for a more strategic approach to procurement by public clients.
This month, Martyn Jones examines how this fresh guidance and legislation provides the opportunity for clients to take a more strategic approach to procurement in delivering their policy objectives.
In essence, the intention is to encourage and support public clients to assemble more strategically aligned supply chains to deliver more innovative, valuable, predictable, and sustainable outcomes.
This more strategic approach to procurement can also be seen as addressing the deep-seated problem in construction – the all-to-often misalignment between the strategies of clients and their suppliers, supply chain relationships and operational practices.
The National Procurement Policy Statement recognises public procurement as a “key lever in achieving the Government’s missions by sourcing goods and services that deliver value for money, including social and economic value across the commercial lifecycle that drives sustainable economic growth and benefits local communities, raising living standards in every part of the United Kingdom”.
The Procurement Act aims to simplify and modernise public sector procurement, promoting efficiency, transparency, and fairness, while encouraging SME and social enterprise participation.
It aims to ensure that public money is spent effectively, promoting economic growth, and delivering social value in line with the government’s 5 missions to deliver a decade of national renewal.
Its key objectives include adopting a simpler and more flexible commercial system with a more streamlined and flexible approach to procurement, making it easier for suppliers to engage with the public sector.
It calls for greater transparency in procurement, ensuring that public spending is transparent and subject to proper scrutiny focusing on value for money, economic growth, and social value.
Then there’s capability – supporting investment in innovation, skills, digital, offsite, quality, and the whole-life performance of built assets, especially in relation to environmental performance and safety.
Also offering a new “competitive flexible” procedure allowing contracting authorities to use more flexible approaches to procurement.
This means public clients can effectively interact with the market and supply chain assets, deploying early market engagement – the process of engaging with suppliers before buying.
What are the benefits of early engagement? Well, it can help generate more innovative and targeted value solutions through a greater understanding of the capabilities and maturity of potential suppliers, as well as revealing the risks and challenges.
It also presents opportunities to not only identify the skills, knowledge, and experience of tenderers but also their behaviours and collaborative capabilities against criteria such as: The maturity of their relationship management approach; their depth and scope of learning and innovation; their leadership; their customer focus; and the effectiveness of their analysis, planning, and problem solving.
This pre-appointment interaction between buyers and suppliers presents the opportunity for developing greater mutual understanding and more open relationships – a precursor to undertaking relationship management in post-appointment project teams and supply chains, as described in last month’s article.
But is market engagement viable for all clients? Well, the decision to adopt it will depend on a project’s desired objectives and outcomes, and the complexity and sensitivity of the works (cladding remediation being a good example of the need for well-developed customer-facing behaviours).
And a word of caution on behavioural assessments. Most projects in construction do not justify or require them as part of the procurement process. It’s not always feasible to invest the time and resources necessary so any early interaction with the market needs to be proportionate to the specifics of each project and its supply chains.
And then many clients may not have the necessary nous needed for meaningful engagement so this could be a role for the client advisor as set out in the CESW and Midlands publication, ‘Client advisor guide’. Less frequent clients may opt for one of the many frameworks, which provide market engagement and more straightforward access to contractors and consultants with the attributes being sought.
Given this new cluster of guidance and legislation, coupled with much previous guidance, such as the Construction Playbook, are we finally seeing a more strategically and operationally aligned way of thinking about procurement in the wide range of very different supply chains that collectively constitute our industry?
Mediation has been very much a part of the dispute resolution landscape in the construction industry for over 30 years. On 1 October 2024, a historic change to the status of alternative dispute resolution in the civil justice system took effect. Amendments to the Civil Procedure Rules (CPR) came into force to promote the use of alternative dispute resolution including mediation. The amendments bring the rules in line with the Court of Appeal decision in James Churchill -v- Merthyr Tydfil County Borough Council [2023].
As a result of the amendments the use of mediation is likely to increase significantly – but when is the best time to mediate?
Gowling WLG, in collaboration with the University of Manchester, are undertaking a ground-breaking research project, the aim of which is to investigate when parties mediate their disputes. What are the influences on the decision-making process? Will the new Amendments to the CPR have any impact on timing?
The start of the research project is a short questionnaire that will enable the collection of data from those using mediation. This will be invaluable to the whole research project.
Take part in the research
To take part, we’re looking for participants with practical experience of the use and timing of mediation in commercial dispute resolution. If you fit the criteria you can answer our survey by clicking on this link. We look forward to your valuable input.
This research attempts to collect data from professionals who have practical experience of the use and timing of mediation in commercial dispute resolution. If you are interested but have no genuine experience, please email the researchers peter.fenn@manchester.ac.uk or obuks.ejohwomu@manchester.ac.uk
You are being invited to take part in an online questionnaire/survey about the use and timing of mediation in dispute resolution. The research is being carried out at the University of Manchester in collaboration with Gowling WLG, a multinational law firm. Gowling WLG’s involvement is limited to circulation of the questionnaire, and they will have no access to the data you provide. In any event the questionnaire is anonymous and confidential and no personal identifiable is collected [we do NOT collect your IP address].
FIND OUT MORE HERE
The Education Landscape Programme, developed by SDN in partnership with The Gatsby Foundation, provides free, independent resources to help businesses navigate and engage with the education sector.
Key Resources:
· The Education Landscape Guide – A clear overview of the education system and how businesses can benefit from engaging with it.
· The Education Landscape Index – A practical tool outlining five key ways businesses can get involved:
1. Supporting Students – Inspire career choices through mentoring and industry talks.
2. Supporting Teaching – Share industry insights to improve education quality.
3. Providing Workplace Experience – Offer site visits, internships, or work placements.
4. Providing Expert Guidance – Help shape curricula to match industry needs.
5. Work-Based Learning – Develop talent through apprenticeships and on-the-job training.
Why Get Involved?
· Access Future Talent – Connect with skilled students and graduates.
· Upskill Employees – Support staff development through partnerships.
· Boost Brand & Influence – Strengthen industry reputation and shape the workforce.
Explore resources & get started: educationlandscape.org.uk
By engaging with education, businesses can help shape the future workforce and bridge the skills gap!
Recently celebrating St Valentine’s Day, triggered Martyn Jones thinking about the importance of nurturing “good” relationships in construction.
For as long as most of us can remember, we have been urged to build better inter-personal and inter-organisational relationships in our project teams and supply chains.
Back in the day, for example, the Reading Construction Forum’s publication, Unlocking specialist potential called for better relationships based on teamwork and greater collaboration. This not only recognised the importance of the relationships between clients, consultants, and main contractors but also reaching out to and including specialist contractors.
Some progress has clearly been made but we still tend to err towards traditional and well-trodden procurement approaches and delivery methods, emphasising price rather than value, and accepting their implicit transactional relationships.
We know it is particularly tricky shifting away from our traditional approach to relationships in construction as we are mainly a project-based industry, with short-term and transitory relationships. Many clients are infrequent who have neither the nous nor inclination to devote time and resources to relationship building.
And, when early attempts are made to build better relationships in a project these can be quickly thwarted when the going gets tough – as is often the case in even the best managed projects – and we end up back in our silos and reverting to more transactional, even adversarial relationships.
This presents a strong case for working on our relationships in construction, as they do in many other industries which, because of the way they operate, often benefit from having longer-term, more transparent, committed, and trusting relationships.
What does the practice of building and maintaining positive relationships between people and organisations involve? To start with, it involves assembling teams having shared behaviours and one aligned culture as well as, of course, having the necessary technical skills and experience.
Then there’s embedding relationship building in the purpose of projects alongside delivering on quality, cost, and programme. And building trust by being respectful in words and behaviours and having open, honest, and deep conversations.
Investing the time, resources and energy needed, admitting weaknesses, culpability and saying sorry. And starting every progress meeting by checking on the health of the relationships and surfacing and continuously addressing the “invisible” reasons why people and cultures so often resist working on relationships, even when traditional interactions clearly aren’t working.
What about the don’ts? These include, don’t keep finding faults and defaulting to managing via the contract rather than the relationships.
Don’t argue on email; always have face-to-face conversations for matters of difference and don’t let egos get in the way of admitting weaknesses, culpability, and saying sorry.
Don’t spend so much time on religiously following systematic processes at the expense of delving deep into what people are thinking and feeling.
Don’t underestimate the time, effort, resources, persistence, and patience needed to bring about changes in behaviours and relationships and don’t ignore what holds us back when it comes to confronting and changing our behaviours.
How do we go about finding out what people really think and feel? In the case of Andrew Goodenough, Infrastructure Director at Bristol International Airport, he commissioned Paul Fox, at Constructive Coaching, to help build better relationships, starting in the pre-contract stage, of one of his projects.
Paul says, “Building a collaborative cohesive team was front and centre along with the necessary investment. The team have met every three months – offsite – to work on the team and its goals, resolving differences and misunderstandings, and growing the mutual confidence to set new goals. This has created a high-performing team delivering a project that’s ahead of programme and under budget.”
Andrew says, “We are in the middle of a £64m project. From preconstruction, we engaged Paul to facilitate regular workshops to help us hold each other to account, keep us on track, and hold open, honest, and sometimes awkward conversations between us as client, consultants, and contracting parties.
We do not leave these workshops until we reset and sorted through any problems together. And it works. We are currently ahead of programme, have positive working relationships and a no bull…t attitude throughout. We have no outstanding compensation events – all being agreed as we go.
We invest heavily in the team and the team ethos, recognising that it takes time to create the necessary trust and culture so that we can have honest, healthy, and constructive disagreements.
I know the team finds it refreshing and I know too that after 30 years in this game I certainly have got a lot out of it and really enjoyed the process.”
Hello and welcome to the March newsletter.
It has already been an exciting to start to 2025 for Constructing Excellence Midlands that has included opportunities for a bit of a look back as well as a chance to look forward.
The Annual Review and AGM provided the forum for an overview of the great work delivered over the previous year and to celebrate the success with our members. It can be quite difficult to sum up all the activities that take place and the collaboration that is enabled through the network but the annual report and the presentations from the Chairman, Chief Executive and the various Clubs, Theme Groups and Forum chairs and representatives helped to give a real flavour of how things have moved forward. I have only been involved for the last six months so I found it incredibly informative, and I was able to take away more understanding and a wider appreciation of what has been achieved as well as the areas of focus going forward.
Before the Annual Review and AGM, we had the opportunity to look ahead at the strategy day which was a chance to look at what we do and how and why we do it. There is an obvious focus on providing value to members to ensure we can retain and grow membership going forward, and certain initiatives that were captured during the discussions already appear to be having a positive impact on our membership. We have strength in numbers, and growing numbers will only strengthen us further. I am encouraged by how a collaborative approach to significant challenges such as skills, sustainability and safety can be addressed more effectively as an industry than if trying to tackle them on our own in our different organisations. It was clear from our discussions on the future strategy of CE Midlands that collaboration continues to underpin everything that we do.
Opportunities to grow networks, make connections and build the foundations for collaboration going forward are coming thick and fast. We have a number of events coming up including the G4C Midlands Awards on 27th March where we are looking forward to celebrating the future stars of the industry, I hope to see you there!
Thanks for taking the time to read my introduction and I hope you enjoy this edition of the newsletter.
Book Your Place for the G4C Awards 2025 – Celebrating the Future of Construction!
The G4C Awards 2025 are fast approaching, the SHORTLIST has already been revealed so now is the time to secure your place at the awards dinner! 
These prestigious awards shine a spotlight on the Young Achievers in Construction and the companies that are dedicated to nurturing the future leaders of our industry. If you are passionate about supporting emerging talent and driving innovation within the built environment, this is an event you won’t want to miss!
Why Attend?
- Celebrate the rising stars of the construction industry.
- Show your company’s commitment to supporting young professionals.
- Network with key industry leaders and like-minded professionals.
- Enjoy an unforgettable evening of inspiration and recognition.
Event Details:
Date: 27th March 2025
Venue: The Burlington Hotel, Birmingham
Secure your place today! Book your tables or individual tickets now by clicking the button below. Let’s come together to celebrate the future of construction! 

Book Now
Ticket Prices:
- Table of 10: £900 + VAT
- Individual: £100 + VAT
- G4C Special Rate: £50 + VAT
(Special rate applies only to G4C members and individuals whose parent organizations are REGIONAL members of CE Midlands.)
Proudly supported by Rider Levett Bucknall (RLB), this event promises an evening of celebration, networking, and recognition.
The CE West Midlands Awards 2025 are back, shining a spotlight on the brightest and best in the region’s built environment sector. Recognised as the premier celebration of best practice across construction, these prestigious awards highlight the core strengths of the industry and the commitment to delivering world-class buildings, housing, infrastructure, and facilities in a collaborative and sustainable manner.
Key Details:
- Entry Deadline: 5pm on Friday, 7th March 2025
- Awards Dinner: Thursday, 1st May 2025 at Edgbaston Cricket Ground, Birmingham.
Why Enter? Winning or even being shortlisted for a CE West Midlands Award is a mark of excellence that sets you apart in the industry. It’s an opportunity to:
- Showcase your achievements and innovative projects to a wider audience.
- Gain recognition from industry peers and stakeholders.
- Enhance your reputation and attract new clients.
- Strengthen relationships with existing partners.
- Boost team morale by celebrating their hard work and dedication.
Who Can Enter? The awards are open to all organisations and project teams involved in delivering buildings and civil engineering projects within the West Midlands. Whether you are a developer, client, contractor, specialist or sub-contractor, engineer, designer, or consultant, if your work contributes to the region’s built environment and exemplifies best practice, we want to hear from you.
Submit your entry now and take your place among the industry’s finest!
Don’t miss the chance to be recognised for excellence in construction across a range of categories:
Building Project of the Year
Client of the Year
G4C Future Leader
Retrofit Award
Regeneration & Conservation
Infrastructure Project of the Year
ESG Award
Innovation Award
Integration and Collaborative Working Award
SME of the Year
Climate Action Award
Residential Property of the Year
People and Culture Award
Delivering Value Award
For all entry forms, please visit https://www.cemidlands.org/about-the-awards-west
CLICK HERE TO DOWNLOAD THE PRESENTATIONS
Highlights from the AGM and Annual Luncheon
Molly Lydia Shaw, Chair of G4C Midlands West. G4C have had a very busy year with lots of events, socials and awards. The shortlist for the G4C Awards 2025 have just been announced so they are also looking ahead to an exciting year ahead.
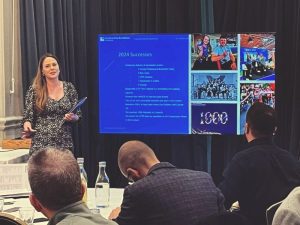
Andrew Carpenter presenting the work being done by the CE Midlands Forums. We have four forums in total with the following areas of focus:
Infrastructure – chaired by Mark Lyddon
Social Housing – chaired by Mike Doolan
Construction Clients – chaired by Darren Bramley
The Industry Stakeholders Forum currently has the following industry body members – CITB, CECA Midlands, Constructing Excellence Midlands, RIBA and Chartered Institution of Civil Engineering Surveyors (CICES)
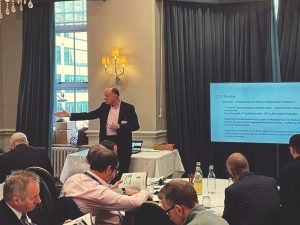
CE Midlands Chair Uma Shanker gave his chairman’s report
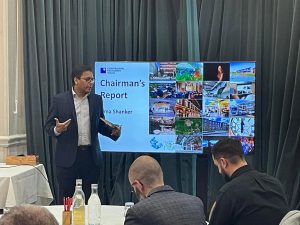
Natasha Heritage, Co Chair of our newly launched Social Value Theme Group. This group are committed to advancing social value in construction, ensuring the industry exceeds its societal responsibilities. It aims to unite stakeholders to drive initiatives that benefit communities, enhance the environment, and boost economic prosperity.
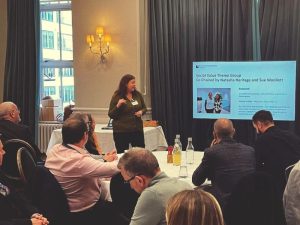
Tom Woodhead MCMI FIC standing in for our Smart Construction Theme Group’s Chair, Dhiran Vagdia.
This theme group’s focus is to share knowledge and foster collaborative working within the digital technology and offsite sectors in the Midlands, signposting work in these fields being done by others.
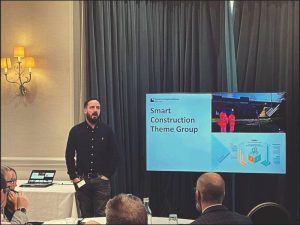
Richard Cymler, Director at Sweco and Chair of our Building Safety Theme Group highlighted the work the Group have done this year.
The Theme Group have published a new Advice note on the Implications of the Building Safety Act during the early stages of Land Development. This can be found on our website under the Resources section.
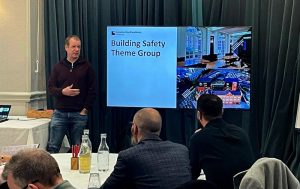
Faye Beaman Associate Director of Arup and Chair of CE Midlands Birmingham and Black Country Club
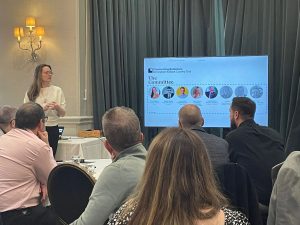
Sophie Leake, Vice Chair of HAWCE (Herefordshire and Worcestershire Club)
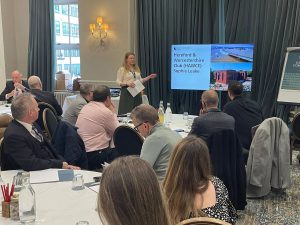
Jasmine Craft, Project Engineer at Viridis Building Services Ltd and Chair of the Lincolnshire Club.
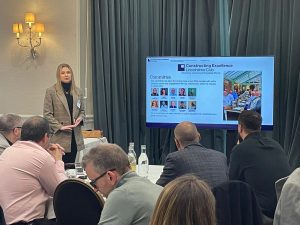